Carpenters health and safety RAMs pack. BEST OFFER
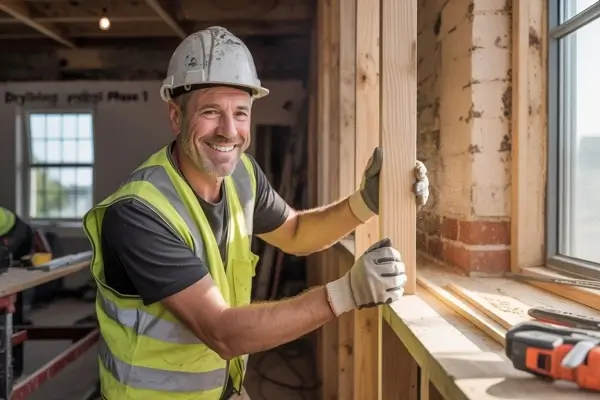
This package is primarily for on-site carpentry companies and not joinery shops. A complete H&S package for just £65.00.
![]() |
![]() |
![]() |
Sample 1 |
Sample 2 |
Sample 3 |
Carpenters are skilled tradespeople who primarily work with wood to construct, install, and repair various structures and items. Their expertise spans several areas, including rough carpentry, which focuses on structural framing, and finish carpentry, which involves meticulously installing cabinets, trim, and other detailed woodwork. Their work encompasses both new construction projects and renovating or restoring existing structures, making them versatile assets in the building industry.
In their capacity, carpenters are responsible for constructing and installing essential wooden frameworks, including walls, floors, and roofs, which provide the foundational structure of buildings. They also perform the intricate tasks of installing and repairing doors, windows, and staircases, ensuring functionality and aesthetic appeal.
Regarding materials, carpenters select, measure, cut, and shape timber and other composite materials precisely, tailoring them to meet specific project requirements and design specifications. This includes installing kitchen cabinets, custom shelving, and various fixtures that enhance the utility and visual appeal of spaces. Many carpenters also take on the creative challenge of designing and building custom furniture that reflects the client’s style and meets practical needs.
In addition to new construction, carpenters possess the skills to repair or restore damaged wooden structures, be it furniture, flooring, or significant historical buildings, preserving their integrity while ensuring adherence to modern standards. Some carpenters may choose to specialise in niche areas such as timber framing, which emphasises traditional methods, cabinet making, which focuses on functionality and design, or trim work, which enhances the elegance of interiors.
Their responsibilities can also include constructing the essential frame of a building, encompassing the installation of key elements like walls, floors, and roofs. Carpenters pay great attention to detail when installing trim, moulding, doors, cabinets, and other interior components, which contribute to the overall character of living spaces. Moreover, they are adept at installing various fixtures, such as doors and windows, and flooring in newly built and existing homes, ensuring seamless integration with the overall design.
Table of contents for carpentry package:
Risk assessments :
01) 1st and 2nd fix carpentry works
02) Risk awareness for areas where asbestos could potentially be discovered
Method statements for:
03) Recommended fixing techniques for various substructures
04) Roof timbers
05) Hanging doors
06) Kitchen fitting
07) Laminate flooring
08) Timber partitioning
09) Fencing
COSHH assessments for:
10) Contact adhesive
11) Decorators caulk
12) Expanding foam
13) Solvent-free grab adhesive
14) Intumescent sealant
15) Silicone sealant
We are pleased to present our exclusive package comprising 15 of our most popular documents for carpenters. We have carefully selected these documents based on our vast professional experience and the download trends of our esteemed customers. This comprehensive package is an electronic document containing 50 pages of all the essential information regarding health and safety regulations in the carpentry industry. By purchasing this package, you will have access to the "Health & Safety Gold Standard Award" that you can proudly display on your website. This award will testify to your clients, customers, and contractors that your health and safety measures are up-to-date and in line with the latest industry standards. Furthermore, we are committed to keeping this carpentry package current and relevant by updating it regularly to keep up with the ever-changing health and safety regulations.
This comprehensive package offers excellent value for money, saving over £70 off the list price compared to buying these documents individually. Trained health and safety professionals have written it, increasing your chance of winning tenders. The document is in docx format, which allows you to edit it in Word™ or any other processor of your choice. You can easily add your company details and logo to the cover sheet, and then it’s ready to go.
This document is recognised by local authorities, principal contractors, and CDM sites and is approved by H&S managers. Our customers' feedback is a testimony to the value of this package.
Carpenters face many risks in the construction industry, including falls from height, slips, trips, and falls. Trips are a high-risk area for carpenters, as there are often trailing leads, toolboxes, screw boxes, and a selection of tools and battery chargers dotted around the work area. There are occupational hazards from inadvertently disturbing asbestos, working with chemicals and wood dust, hearing loss, and hand-arm vibration risks from certain power tools. Carpenters are at risk of cuts, grazes, and amputations from hand and power tools, as well as strike injuries to the eyes, face, and body from objects ejected by a tool's moving parts. Handling materials, working in confined spaces, or carrying out repetitive tasks can cause musculoskeletal complaints, and dermatitis can be standard from using adhesives, silicones, and solvents. In short, carpenters are at a higher risk of injury than many other trades due to the amount of power tools used and the versatility of the work.
If you are an employer with a workforce of five or more individuals, you are legally obligated to have a Health and Safety policy. Moreover, it is essential to carry out risk and COSHH assessments to ensure your work environment is safe. While method statements are not a legal requirement, they are crucial if you seek work with principal contractors or CDM sites. Failing to provide method statements may negatively impact your chances of securing the job.
A Company Health and Safety Policy: If you are an employer with a workforce of five or more individuals, you are legally obligated to have a Health and Safety policy. Moreover, it is essential to carry out risk and COSHH assessments to ensure your work environment is safe. While method statements are not a legal requirement, they are crucial if you seek work with principal contractors or CDM sites. Failing to provide method statements may negatively impact your chances of securing the job.
Risk assessments: Every task must be completed before an employee carries out any work. They are conducted to discover potential hazards and, if necessary, introduce control measures to eliminate or reduce the risk to an acceptable level.
Method statements: Method statements don’t have to list every job stage because many fitments come with their method statement. For example, if a carpenter fitted a lock, he would fit it per the manufacturer's instructions. The manufacturer's instructions are, in effect, a method statement.
COSHH assessments: COSHH assessments are a legal requirement for any substance used in the workplace. They must inform people of the composition, the product hazards for the user and the environment, fire fighting measures, and first aid measures.
For several years now, the Health and Safety Executive (HSE) has recognised the effectiveness of online training and considered it as one of the most time-efficient options for many workforces. One of the main benefits of online training is that employees can take a course at their own pace and convenience. Unlike a traditional classroom setting, where all relevant staff members have to be present simultaneously, online training allows individuals to learn and progress at their own pace. This makes it an ideal option for busy workforces looking to upskill their staff while maintaining productivity.
Some relevant online training courses for carpenters available from HSEDocs include:
- Manual Handling
- Asbestos Awareness
- Work at Height
- Slips, Trips and Falls
Carpenters require comprehensive training in four essential courses to master their craft. However, training for carpenters primarily involves repetition, instilling positive attitudes, and disseminating information on newly introduced working practices. To accomplish this, there are several ways to impart knowledge, such as verbal communication, the distribution of safety fliers, the posting of notices on notice boards or work areas, the dissemination of new method statements, risk assessments, and Control of Substances Hazardous to Health (COSHH) assessments. A toolbox talk can also be conducted to convey the message about any potential risks to the individuals who perform the work. The most crucial aspect of any training is ensuring that the message is communicated effectively and that all individuals know the potential risks involved.
GET THIS DOCUMENT
£65.00+VAT
- Available in Word™
- Fully customisable
- Add your Company Logo
- UK & EU Compliant