Manual handling. Not just about lifting boxes.
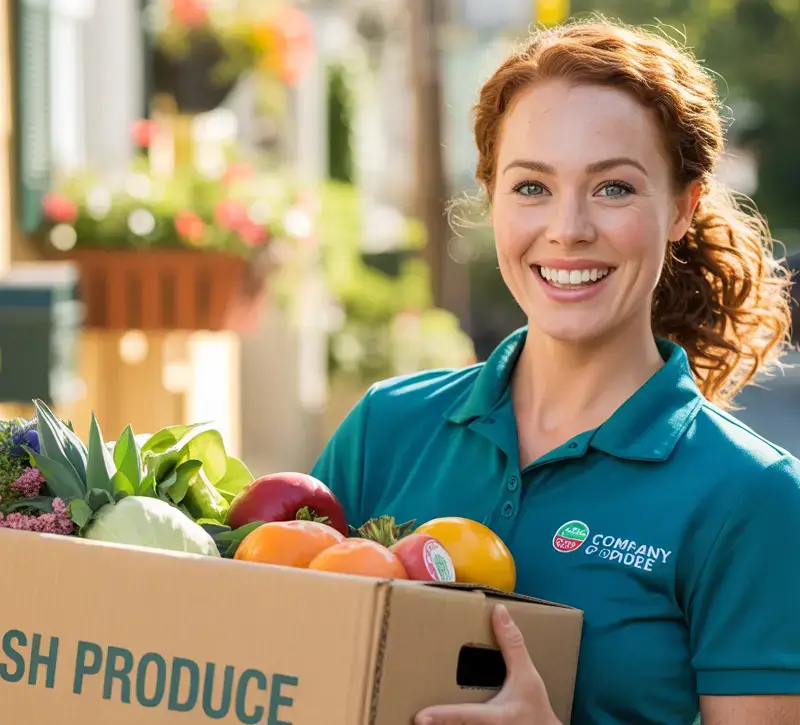

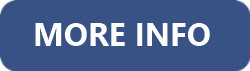
Manual Handling. It’s Not Just About Lifting Boxes
Previously, manual handling training in a traditional classroom setting often involved candidates demonstrating the proper way to lift a box to obtain their manual handling certificate. However, this approach led to overconfidence and a false belief in candidates that they were fully trained in physical manual handling techniques.
Manual handling involves many tasks such as pushing, pulling, carrying, lifting, lowering, passing, bending, twisting, and stretching, including lifting boxes. It's impossible to cover every physical example of every manual handling test in a single exercise. For instance, showing someone how to push a box along the floor differs from moving a wheelbarrow on uneven ground or mowing a lawn.
Consequently, health and safety now dictate that manual handling training should consist of classroom or online training, which focuses on how the body works, accident and injury rates, etc..… and workplace training, which consists of individuals being shown or told the correct way to handle objects relevant to the worker's tasks and environment at their workplace.
Recognising the vast array of manual handling activities is crucial in understanding the scope of potential risks and the measures necessary to mitigate them. The range of manual handling tasks is vast, encompassing lifting and moving objects and extending to pushing, pulling, and stabilising different loads.
Each task presents challenges and requires a distinct approach to minimise risk and enhance efficiency. For example, moving a trolley filled with goods differs from manually handling or repositioning a patient in a healthcare setting.
Moreover, manual handling isn't limited to physically moving items; it also includes tasks that involve holding items in a static position, twisting, or bending while handling loads. The nature of the item, whether bulky, heavy or awkwardly shaped, adds another layer of complexity to manual handling tasks.
These activities are present across various sectors, from construction sites where materials must be regularly moved to office environments where reorganising workspace or handling deliveries are common occurrences.
The Manual Handling Operations Regulations 1992 are a key piece of legislation that employers must observe. It states that its purpose is to explain how to avoid, assess, and reduce the risk of injury from manual handling.
Manual handling training is not just about the weight of objects. There are other significant risk factors that we need to be aware of.
Awkward postures when moving or supporting loads can significantly increase the likelihood of musculoskeletal disorders. Repetitive movements, especially those involving twisting or bending of the back, can further increase the risk, leading to strain over time that may cause chronic conditions.
Inadequate rest intervals during manual handling tasks can worsen workers' physical strain, reducing their ability to perform tasks safely and efficiently. Understanding and being cautious about these risk factors is crucial for maintaining a safe work environment and ensuring our own well-being.
Equally important is considering the individual's capacity and the environmental conditions under which manual handling tasks are performed. Personal factors such as fitness level, health status, and pre-existing conditions or injuries can influence one's susceptibility to manual handling injuries. Environmental elements, such as confined spaces or uneven flooring, can hinder the execution of tasks using optimal postures and techniques, thereby increasing the risk of accidents and injuries.
Mastering correct techniques is crucial for reducing the risk of injury during manual handling tasks. Strategies such as maintaining a straight posture, using the strength of the legs instead of the back for lifting, and keeping the load close to the body can significantly lower the risk of musculoskeletal damage. Additionally, it's essential to have a stable support base by evenly distributing weight through the feet and avoiding twisting movements while carrying loads. These practices are necessary for all forms of manual handling, whether moving objects within an office environment or more physically demanding tasks on construction sites. Employers are responsible for providing training sessions that focus on these techniques, as well as on the proper assessment of loads and recognising when to use mechanical aids or seek assistance.
Employers must navigate legal requirements to maintain a high safety standard in manual handling operations. Regulations require organisations to conduct comprehensive risk assessments to identify potential manual handling hazards and develop strategies to mitigate these risks. In addition, the legislation requires employers to provide thorough training to employees on safe manual handling techniques.
The Manual Handling Operations Regulations (MHOR) 1992 represent a crucial element of the UK's health and safety legislation, explicitly targeting the risks associated with manual handling tasks in the workplace. These regulations compel employers to conduct thorough risk assessments of manual handling activities, identify potential hazards, and implement suitable control measures to minimise the risk of injury to employees. Key to these measures is providing adequate manual handling training tailored to the needs of the workforce and the specific tasks they undertake.
Under the MHOR, employers must avoid manual handling activities where reasonably practicable. If such tasks cannot be avoided, they must assess the risks associated with these manual handling operations and take appropriate action to reduce the likelihood of harm. This includes redesigning tasks to avoid hazardous manual handling, providing mechanical aids, or implementing safer manual handling techniques.
Training plays a pivotal role in this framework, which aims to equip employees with the knowledge and skills to perform manual handling tasks safely. It should cover the correct lifting, carrying, pushing, and pulling techniques and the understanding of how manual handling risks can be assessed and mitigated in their work environment.
Employers must ensure the training is understandable and relevant, allowing employees to apply safe manual handling principles in their day-to-day roles. Failure to comply with the MHOR 1992 can lead to significant legal and financial repercussions for businesses, including fines, prosecution, and increased liability in the event of workplace injuries. Hence, adherence to these regulations is not only a legal obligation but a practical necessity for maintaining a healthy and safe working environment.
Ergonomics is crucial in reducing the risk of injuries associated with manual handling tasks. Adjusting work environments and equipment to the worker's needs can substantially minimise strain on the body, thus improving safety and productivity. This approach involves adapting the height and position of workstations to encourage a natural posture, designing comfortable tools for extended use, and arranging the workspace layout to allow efficient movement without unnecessary bending or twisting. Moreover, ergonomic assessments can pinpoint specific areas needing adjustments, customising the workplace to fit the physical requirements of its users.
Incorporating an ergonomic approach to manual handling tasks ensures that the environment and the manual handling procedures used are safe.