What are RAMS in Construction?
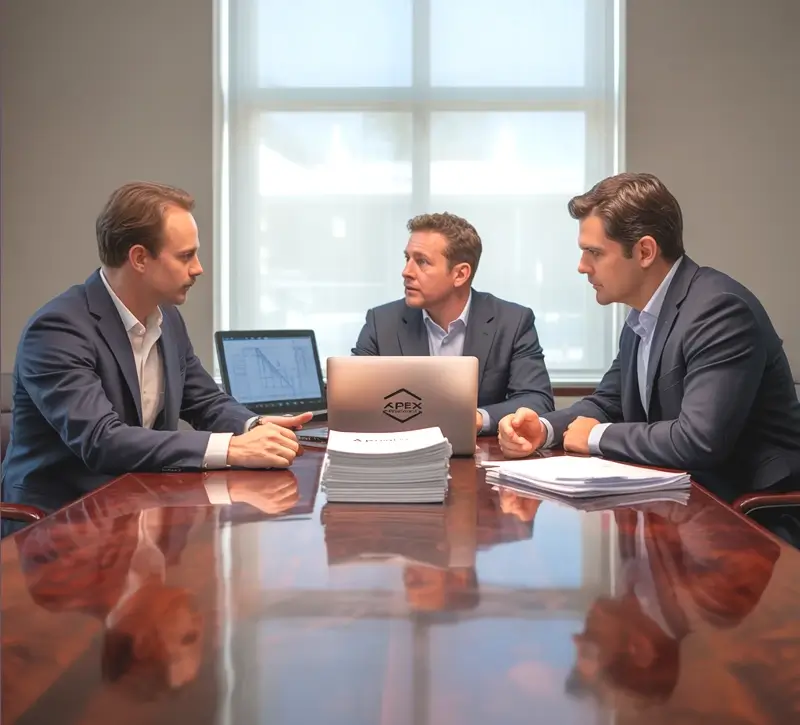
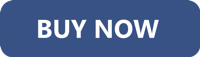
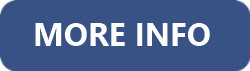
What are RAMs for the Construction Industry?
In the construction industry, it is paramount to prioritise the safety of both workers and the public. Risk Assessments and Method Statements (RAMS) are essential to achieve this goal. These comprehensive H&S documents provide a detailed overview of the potential hazards associated with a construction project and outline the specific methods and procedures that must be followed to minimise or eliminate these risks. Although we often associate RAMS with Risk and Method Statements, they are more encompassing than just these two types of documents, as the term is more often used as a substitute for a company's health and safety file.
The health and safety file should include all H&S documents required by the principal contractor or the Construction (Design and Management) Regulations. The list of documents is as extensive as the principal employer demands and may consist of.
- Lone worker policies.
- Company H&S policy.
- Modern slavery policy.
- Equality and diversity policy.
- Equal pay policy.
- Staff training records.
- Environmental policy.
- Induction records.
- Safety permits.
- Work in confined spaces documents.
- COSHH Assessments.
- Toolbox talk matrix.
The list of H&S documents contained within a company's RAMS is not set in stone. It changes and evolves to suit current situations and highlights specific attitudes on which a principal contractor may base their values. This dynamic nature of H&S documents underscores the need for continuous learning and adaptation in the construction industry. Therefore, some principal contractors insist on equal pay policies, while others do not. Likewise, COVID-19 policies essential in the early 20s are now largely redundant.
The Benefits of RAMS for Construction
When bidding for construction work, an aspect that can either pose a challenge and serve as a foundational requirement is the management of the numerous construction-related documents or RAMS, particularly those related to health and safety (H&S). These RAMS are far more than mere formalities; they are vital for ensuring compliance with established regulations and industry standards. Their preparation is a testament to your unwavering commitment to the safety and well-being of both your workforce and the surrounding community. However, a pertinent question arises: does the substantial investment of time and effort required to understand and compile these documents ultimately yield worthwhile returns?
In the competitive landscape of construction tendering, submissions that thoroughly substantiate a company's commitment to health and safety through detailed and well-organised documentation enjoy a significant competitive edge, mainly when directed towards larger organisations. Conversely, it is unlikely that a local contractor seeking to hire a painter for a week might require an exhaustive equal-pay policy. That being said, having an established equal-pay policy not only demonstrates your commitment to equitable practices but also provides your company with a competitive advantage, even in smaller, localised projects.
A robust commitment to RaMS and H&S practices not only enhances the likelihood of success in securing tenders but also sets a positive precedent for the project's execution. It nurtures trust and confidence in a company from the outset. In recent years, the construction industry has increasingly prioritised safety and compliance with regulatory standards as key criteria for awarding projects. Therefore, a tender that effectively showcases a strong commitment to health and safety becomes markedly more appealing, aligning with the industry's focus on safety protocols and compliance requirements.
When faced with a principal contractor that demands the inclusion of a comprehensive Health and Safety (H&S) file within your tender submission, it may be strategically beneficial to present your pricing as a three-tiered structure. For instance, your bid could clearly outline costs reflecting an intentional allocation of a percentage—say 15% to 20%—above your standard pricing. This transparent approach helps the principal contractor recognise that a portion of your profits and turnover is dedicated to H&S initiatives. While this pricing strategy may initially appear higher, it is fully justified and communicated through your firm's commitment to health and safety, as well as adherence to best practices, which the principal contractor explicitly seeks.
- Site costs. (Labour/materials/site management)
- Transport/office/overheads.
- H&S
RAMS and Construction Phase Plans
Central to the effective management of construction projects, Construction Phase Plans (CPPs) are indispensable instruments designed to coordinate health and safety efforts throughout construction activities. Mandated by the Construction (Design and Management) Regulations 2015, these documents provide a structured framework for addressing the numerous health and safety considerations that arise from the onset of a building project.
The core of a CPP encompasses a thorough articulation of health and safety strategies specifically tailored to address the unique complexities and challenges inherent to each project. It serves to delineate the allocation of responsibilities among various interested parties, ensuring that every individual involved—be it project managers, contractors, employees, or site visitors—understands their specific health and safety duties. This clarity is paramount for ensuring accountability and promoting a culture of health and safety on site.
Moreover, the CPP specifies the mechanisms for risk identification and mitigation. It outlines detailed procedures designed to eliminate or control potential hazards associated with construction tasks, therefore minimising accidents and injuries. This proactive approach not only complies with legal regulations but also promotes the development of a safety-oriented culture within the workforce, emphasising the importance of anticipating risks before they manifest as real incidents.
The CPP also establishes protocols for regular safety briefings, training sessions, and risk assessments, which are vital for keeping all parties informed and engaged in safety practices.
Ultimately, the Construction Phase Plan is not merely a regulatory document; it is a strategic tool that guides the project through its various phases, consistently prioritising the needs of all participants. By ensuring that safety considerations are interwoven into the fabric of project planning and execution, the CPP proves to be a linchpin in the overall health and safety management framework within the construction industry.his proactive approach not only complies with legal mandates but also champions the development of a safety-oriented culture within the workforce, emphasiziemphasisingrtance of anticipating risks before they manifest into real incidents.
Here's a breakdown of the typical content of a Construction Phase Plan (CPP):
Project Outline
Project Description: This section provides a comprehensive overview of the project, including the geographical location, anticipated start and completion dates, and a detailed summary of the scope of work involved. It outlines the project's main objectives, the significance of the work in terms of community impact, and provides any relevant background information that gives context.
Client and Contractor Information: This includes detailed identification of the client and principal contractor, featuring full names, physical addresses, phone numbers, email addresses, and key contact individuals for both parties. This information is crucial for maintaining effective communication throughout the project's lifecycle.
Project Team: A list of key project personnel, encompassing roles such as the project manager, site supervisor, safety officer, and other critical support staff. Each entry will include the individual's name, job title, responsibilities, and direct contact information to facilitate streamlined communication.
Health and Safety Goals: A definitive outline of the project's health and safety objectives, highlighting the commitment to achieving a zero-accident workplace. This section outlines the strategies implemented to maintain health and safety standards and foster a culture of safety among all project stakeholders.
Management of Work
- Management Structure: A detailed diagram or description of the management hierarchy that delineates roles, responsibilities, and lines of communication on site. This ensures clarity regarding authority and accountability throughout the project's execution.
- Communication and Consultation: A clear outline of established procedures for effective communication, including the frequency and format of regular site meetings, consultation forums with the workforce, and methods for addressing concerns or suggestions from team members.
- Site Rules: A comprehensive list of site-specific rules and safety protocols that all personnel must adhere to. This includes emergency evacuation procedures, mandatory personal protective equipment (PPE), and other relevant safety measures to protect workers on site.
- Welfare Facilities: Detailed information regarding the welfare arrangements established for workers, including the location and condition of sanitation facilities (such as toilets and handwashing stations), rest areas, vending services, and access to fresh drinking water.
- Site Induction: A thorough outline of the procedures for inducting newcomers to the site, detailing the topics covered during induction sessions, such as health and safety policies, emergency protocols, and site-specific rules to ensure full compliance and awareness.
Risk Management
- Risk Assessments: In-depth evaluations of potential hazards associated with the project, including physical, chemical, biological, and ergonomic risks. Each assessment will include an analysis of the probability and severity of incidents, categorised into levels.
- Control Measures: A detailed account of specific risk control measures implemented to eliminate or minimise hazards. This will include engineering controls, administrative solutions, and the use of personal protective equipment to ensure the safety of workers.
- Work Activities: A description of specific work activities involved in the project (e.g., working at height, excavation, lifting operations) along with related risks and control measures. Each activity will be analysed for its safety implications and the procedures employed to mitigate risks.
- Monitoring and Review: A systematic approach to monitoring health and safety performance, including regular evaluations of risk assessments and safety protocols. This section will also detail the reviewing process for the safety plan, ensuring it remains current and effective.
Emergency Procedures
- Fire Safety: Comprehensive information regarding fire prevention methods, including the installation of fire extinguishers, employee training on fire safety, and established procedures for evacuation in the event of a fire.
- First Aid: Clear procedures outlining the arrangements for providing first aid on-site. This includes identifying trained first aid personnel, locating first aid kits, and ensuring access to emergency medical services.
- Accident Reporting: A structured process for promptly reporting and documenting accidents and near misses, including forms to be completed and a timeline for reporting. This section reinforces the importance of learning from incidents to prevent future occurrences.
Other Important Considerations
- Plant and Equipment: Guidelines for the safe use, maintenance, and inspection of construction machinery and equipment, ensuring compliance with manufacturer specifications and legal regulations to prevent accidents.
- Waste Management: Detailed procedures for the responsible management of construction waste, including sorting, recycling, and disposal methods to minimise environmental impact and adhere to regulations.
- Traffic Management: An outline of traffic management plans designed to promote safe vehicle and pedestrian movement in and around the site. This includes signage, barriers, and designated pathways to protect workers and the public.
- Design Changes: A systematic approach for managing and documenting changes to project designs during construction, ensuring that all alterations are assessed for safety implications and that necessary adjustments to risk assessments and procedures are made.
- Health and Safety File: Information on the maintenance of a comprehensive health and safety file throughout the project, documenting all health and safety-related activities, incidents, and protocols for reference in current and future projects. This file serves as a permanent record to inform stakeholders and support ongoing safety management efforts.
The CPP is a dynamic document that should be reviewed and updated throughout the construction phase.